For Donald E. Oberg, the company’s founder, it was a passion for both innovation and precision that provided the foundation for success. Oberg pioneered the use of tungsten carbide components in the manufacture of high-speed stamping dies and is widely recognized for revolutionizing manufacturing in the process. In 1985, Mr. Oberg was commended by American Machinist magazine for his significant contribution to manufacturing. That same year, Inc. magazine published an article, The Lord of Discipline, detailing Oberg’s unusual style of management as a driver of company growth.
Over the years, the company has developed an international reputation for thriving on challenges and solving a wide range of engineering problems. Today, while Oberg is quite a different company than the one Mr. Oberg originally started, our passion for precision manufacturing is still just as strong. Our breadth of expertise enables us to provide cost-effective manufacturing solutions for the most demanding and complex production challenges for customers across the globe.
A highly trained workforce plays a pivotal role in our ability to produce high quality parts. Mr. Oberg developed one of the industry’s earliest apprenticeship programs in the 1950’s to help create future generations of highly skilled craftsman that were needed for the fast-growing company. Today, Oberg’s world-renowned apprenticeship program is competency-based involving both classroom and paid, on-the-job skills training.
1948
Oberg Manufacturing Company is established by Donald E. Oberg in Tarentum, PA with twelve employees. It’s the first to utilize tungsten carbide in the stamping die industry.
1950s
Oberg outgrows its original building and relocates a few miles north to Freeport, PA. Mr. Oberg introduces his first-of-its-kind apprentice program to meet the demands of a growing industry.
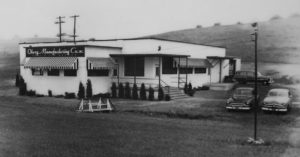
1960s
Oberg expands business to include machining and grinding of tungsten and steel components. It becomes a major supplier of tooling for growing food and beverage can manufacturing.
1970s
Oberg introduces CAD technology into the engineering department and purchases one of the first wire EDM machines used in North America.
1980s
Growth continues with Oberg Manufacturing renaming itself Oberg Industries to better represent its expanding capabilities and the various markets it now serves. It develops electronic die monitoring equipment to measure product quality and track stamping press production processes.
1990s
Oberg establishes a second stamping facility in Sarver, PA and adds 25,000 sq. ft. of manufacturing and office space at Freeport headquarters. It introduces hand-assembly and automated assembly services for components from design through production. The company receives ISO 9001, ISO 9002 & QS 9000 certifications.
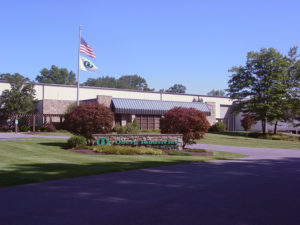
2000s
The company creates an “Oberg Medical” division to handle specific demands from the growing medical market and establishes a new production facility in Costa Rica to accommodate global growth. It adds 100,000 sq. ft. to the Sarver stamping facility to meet growing production demands, and adds multi-axis machining and turning centers to enable flexible manufacturing capabilities for the medical, energy and other markets.
2010s
Oberg adds an 80,000 sq. ft. precision machining center next to its Sarver stamping facility to accommodate its expanding medical division.
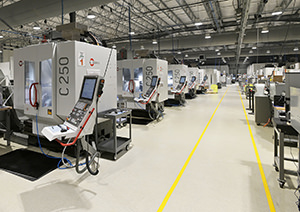
2020s
Oberg acquires XL Engineering, a specialty medical device manufacturer in Elk Grove Village, IL and, in 2020, expands it into 70,000 sq. ft. medical machining facility minutes from Chicago O’Hare Airport to add production capacity.
In August 2020 Oberg acquires Broad Peak Manufacturing, a high-precision surface preparation and finishing facility in Wallingford, CT, to complement its medical device and OEM support capabilities.
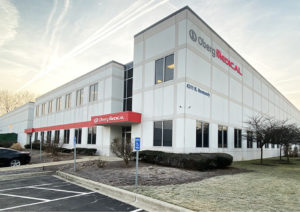